Special Welding
Plasma Transferred Arc Welding, the PTA process is used in instances of extreme demands on wear resistance. A high strength metallurgical bond is formed between the super alloy coating overlay and the underlying component, ensuring that the coating isn’t impaired, even under the highest of stresses.
Applications
- This technology is the best welding solution for valves, seats etc. For Stelite, Nimonic, Inconel and Hasteroy. Plasma technology solves a number of welding problems.
- Metlockast welding procedures, materials, and technicians’ qualifications have all been approved by LR. All the reconditioned parts have LR certificates as per customers’ requirements.
Plasma PTA
The PTA Technology guarantees high efficiency, quality and speed in welding. Excellent surface at low coating volume, high thermal energy of plasma arc using powders as filter materials.
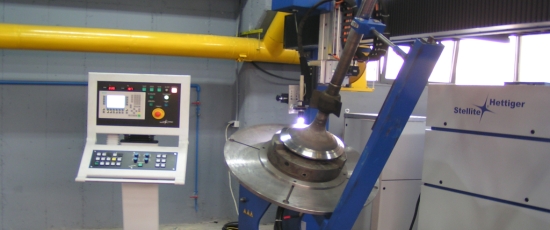
HVOF Plasma Spray
Thermal spray coatings are used to enhance, salvage and improve component life, competing with surface treatments such as chrome plating or heat treating. High Velocity Oxygen Fuel (HVOF) thermal spray process is the leader providing well bonded, high-density coatings with high hardness, delivering outstanding performance in aggressive wear and corrosive environments. The benefits of HVOF are:
- Very Dense Coatings
- Excellent Bonding
- Minimal Temperature Effects
Application parts
Exhaust / inlet valve stem , Rotors etc.
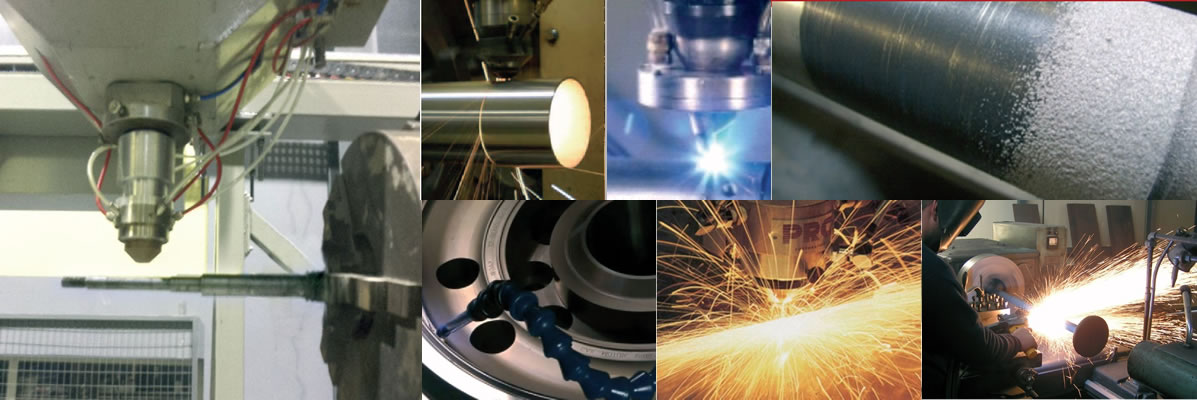
Laser Welding PRC – Laser Cladding
Laser welding, provides the most advanced automated welding technique of continuous operation for the most precise and demanding weldings and also for materials with high melting points or high conductivity. For Shaft, Piston Rods, Turbos and Valve stems.
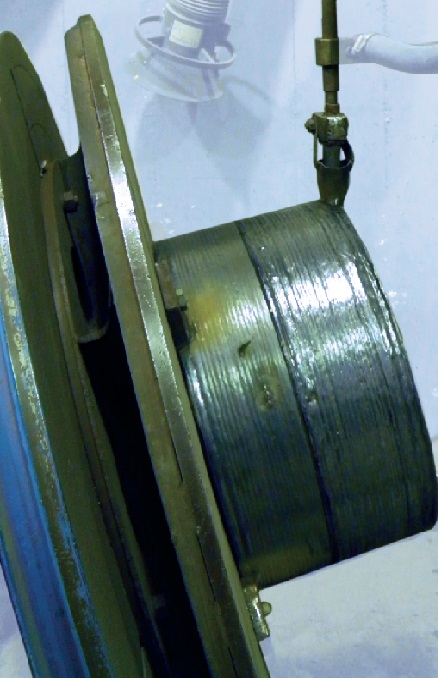
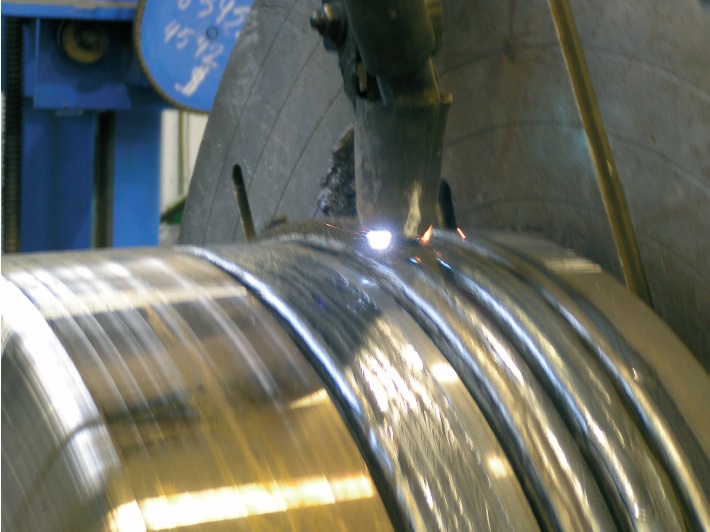
Submerged arc welding (SAW)
Sub-Arc welding is a common arc welding process. It requires a continuously fed consumable solid or tubular (flux cored) electrode. The molten weld and and the arc zone are protected from atmospheric contamination by being “submerged” under a blanket of granular fusible flux consisting of lime, silica, manganese oxide, calcium, fluoride and other compounds.
- High deposition rates
- High operating factors in mechanized applications
- Deep weld penetration
- Sound welds are readily made (with good process design and control)
Advantages
- High speed welding
- Minimal welding fume or arc light iseitted
- Carbon steels (structural and vessel construction)
- Low alloy steels
- Stainless steels
- Nickel-based alloys
- Surfacing applications (wearfacing, build-up and corrosion resistant overlay of steels)
- Less distortion
Parts application
- Piston Crown, Piston Rod etc.
MIG Welding
TIG Welding
Palm Welding